
Size: my boards are pretty small for now and space is always tight so this is just the right size, vs a toaster oven.Sometimes I’ll nudge a part (with a tweezer) that was probably bumped at some point. Visibility: I like being able to watch the board cook.Precise temperature control: given that I can exactly control how many heating cartridges, where they are placed and how much power I apply to each it’s possible to get an exact temperature profile.It does work with double-sided boards, which this hot plate does not.
/www.brokking.net/images/hot-plate/hot-plate_media_image_3.jpg)
It also suffers from inability to easily watch the process. Again, this had problems with uniformity and heating and cooling rates. This seems to be the ‘hacker’ choice with lots of home-built computerized control systems. I bought the cheapest hot plate on Amazon and my opinion was that it didn’t heat fast enough, it wasn’t at all uniform temperature, it didn’t cool fast enough, and finally it was really poorly built and dangerous (like it had a grounding strap inside that wasn’t connected to ground). This is the quicky ‘oven’ of choice for folks like Sparkfun. Alternativesīefore getting into the hot plate, a short discussion of alternatives. Melting temperature must be exceeded by approximately 20 ☌ to ensure quality reflow. Solder reflow is accomplished in the reflow zone, where the solder paste is elevated to a temperature greater than the melting solder point. The dryout section is used primarily to ensure that the solder paste is fully dried before hitting reflow temperatures. The most critical point in the preheat section is to minimize the temperature rise rate to less than 2 ☌/second, in order to minimize thermal shock on the semiconductor components. Reflow curves showing safe ranges and results of bad curvesĪ typical profile consists of a preheat, dryout and reflow sections. Below is a generic reflow temperature curve (courtesy STMicroElectronics): The temperature across the circuit board should be uniform during the phases.
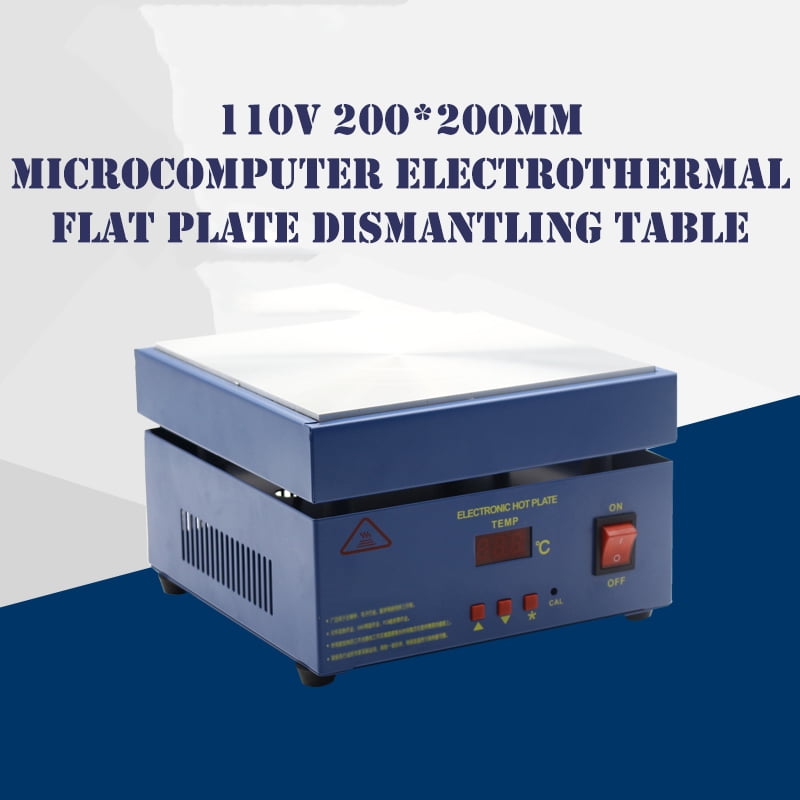

There’s a startup issue so it’s kind of kludgy but it works reliably.
Solder reflow hot plate code#
The source code for the hot plate is here. I ended up with a simple unit made up of a Raspberry Pi controller that used two easy to obtain heating cartridges and the results are outstanding. This is a pretty long article so the results are first. So, I’m building my own reflow hot plate from scratch.Ī reflow oven is a device for melting solder paste on a circuit board such that the paste smoothly melts and surface mount components self-align. I looked into buying a reflow oven but after reading reviews of inexpensive ovens - poor temperature regulation, bad interfaces, dangerous construction - and looking at alternatives (hot plates, toaster ovens, …) I finally just decided that nothing had the necessary attributes. I’ve been building surface mount circuit boards by hand with a hot air gun.
